|
Pellet build-up, layer by layer, around a given starting core.
|
|
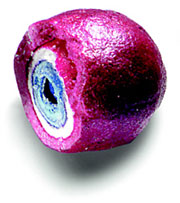 |
Powder Layering
.
|
Suspension and solution layering.
|
Product
advantages. Round pellets, often with a separating layer for
innovative and demanding forms of medicine with high amounts of active
ingredient.
|
|
Comparison. Higher density than spray granulates and agglomerates.
Pellet diameter. Between ca. 0.6mm and
2.5mm.
|
|
Principle of the powder layering process
|
|
|
Principle of the suspension and solution layering process
|
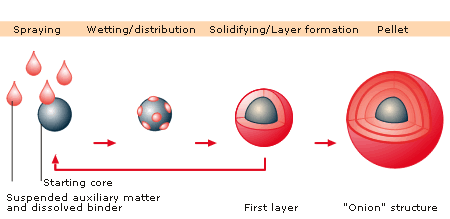 |
|
A starting grain or a pellet can be presented as the starting material. The
pellet is built up to the required grain size by adding the layering substance
one layer at a time. Powder and binders, suspensions or solutions make
suitable layering substances. The layers are densely applied due to the movement
of the pellets in the rotor (-> Fluid Bed
Pelletizing in the rotor). Different layers of various types can be
applied. Thick layers can be applied to the starting grains, which, in the
case of layers containing active ingredients, allow large amounts of active
ingredient to be incorporated.
|
|
Product characteristics
|
Layered pellet
|
Dust free
Round pellets
Good flow behaviour
Easy to dose
Compact structure
Low hygroscopicity
High bulk density
Dense, uniform surface
Narrow grain size distribution
Low abrasion
High active ingredient content possible
Optimum starting shape for subsequent coating
|
With suitable additives, pellets can be made into tablets or used to fill
capsules. The round shape is ideal for uniform coating. Pellets are good for
automatic dosing.
|
|
Manufacturing options
For this process, Glatt offers Batch Fluid Bed Systems with batch sizes
from 500g to 250kg/batch. |
|
|
|